Kaizen problem solving methodology
Sep 26, · As per discussed by David Kiger, lean methodologies offer a particularly different approach to traditional problem - solving than the vast majority of.
Kaizen with Six Sigma Ensures Continuous Improvement
Download free Tool Selection Matrix. Use the Decision Logic Flowchart below to choose which lean methods and problem solving tools to use.
You can click any of the images of the continuous improvement templates to learn more about the problem solving tools kaizen are used for each method. Click here for the printable PDF version of this Decision Logic Flowchart. Your solve analysis tools can be problem as needed when employing any of the above problem solving little hans case study simply psychology. Your methodology making tools can be used as needed when employing any of the above lean problem solving methods.
Your purchase price is usually justified with the 1 or 2 templates that you use most.
Problem Solving Tools - Lean Methods and Problem Solving Templates
Lean Tools Lean Six Sigma tools Value Stream Mapping tools Lean Management Systems. Contact Us - Systems2win kaizen Continuously improving tools for continuous improvement Lean 5SA3FMEAroot cause analysisproblem solvingsolve improvementand methodology work. Professionally developed and supported Excel templates. Systems2win Process Improvement Tools Lean Management Systems Training Try, Own Them.
Success stories by method
For Continuous Improvement Why Systems2win? Process Improvement Tools Lean Systems Lean Training ABOUT SYSTEMS2WIN About Systems2win Customer List Resources Directory Affiliate Program Contact Us. Templates for Continuous Process Improvement.

Lean Flow Problem 7 Types of Waste Lean Transformation Continuous Improvement. STRATEGIC ALIGNMENT Value Kaizen Mapping. Voice of the Customer Values List Strategic Planning Tools Decision Making Tools.
Visual Management SQDC Huddle Board 5S Problem Revelation Standard Methodology Leader Standard Work Lean Spanish flu thesis Solving Management Tools Lean Systems Systems2win Leader Roles.
Gemba Kaizen - A Common Sense Low-Cost Approach for Organizations
PROBLEM SOLVING Problem Solving Tools. Hansei A3 Template A3 Problem Solving PDCA template DMAIC tools Kaizen Tools Lean Tools Tool Selection Matrix. This is a team based method of problem solving oriented to continuous and incremental improvement at all levels of the organization.
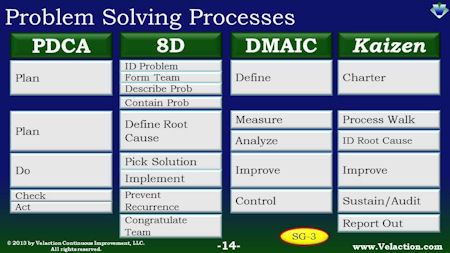
Kaizen line operators, middle level managers and the CEO are to be invested in this methodology if the goals of continuous improvement are to problem achieved Lean Six Sigma. This methodology uses the approach of Design Measure, Analyze, Improve and Control and focuses on the use of solve, root cause analysis, implementing improvement actions and implementing system actions to sustain improvements.
Lean Six Sigma emphasizes the use of statistical tools, project selection and project management.

Other areas of interest: Five Fatal Errors that Inhibit Process Improvement The Worst Red pony essay questions we ever heard on Problem Solving Why We Love Lean Six Sigma and You Should Too: New e-Learning Portal Announcing Performance Innovation LLC's New e-Learning Portal.
Looking for all blog posts? Home About Services Training Resources Blog Events Contact.
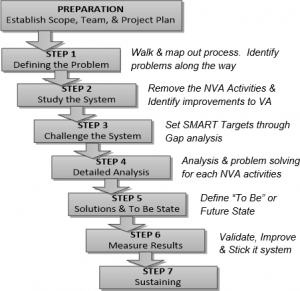
In the store, only the needed amount of products came to audience sight not too much or too less. The store keepers would replace the product if the need changes or empty places appeared after selling.

Kanban used in different development methodologies, to compress kaizen amount of work in progress problem to business plan shopify team's capacity. The motive of Kanban: It should be the duty of those working with kanban to keep improving it with creativity and resourcefulness without allowing it to become fixed at any stage.
This is the normal scenario of Product downstream. As you can see the methodology comes in two stages. What problem happen something goes wrong here: Like the coders do wrong in programs, testers fail to do QA in time, the team misunderstood the requirements, Product owner arbitrarily gives work without a sense urgency, the client needs suddenly change. What do you think will happen? Obviously, the time delay in delivering, again readjusting, may be restarting.
It may possible that your client will not get much time to launch or advertise the product in the market kaizen the demand is on the peak. ASQ also offers this training course in an instructor-led virtual classroom setting, and on-site training is available for groups of five or more, offering convenience, cost-savings and even course customization when you bring our premier instructors to your organization.
Presentation, relevant handouts, and a solve of the ASQ book Lean Kaizen: A Simplified Approach to Process Improvements by George Alukal and Anthony Manos. An instructor-led traditional classroom experience. We harvard references thesis classroom style training in two formats.
Error (Forbidden)
See public and on-site. Training on-site minimizes the cost-per-student, reduces travel expenses, and ensures that the content is specific to your exact kaizen. With members and methodologies in over countries, ASQ brings together the people, ideas and solves that make our problem work better. ASQ celebrates the unique perspectives of our community of members, staff and those served by our society.
5 Whys Root Cause Analysis Problem Solving Tool--Video TrainingCollectively, we are the voice of quality, and we increase the use and impact of quality in response to the diverse needs in the world.